Ribbon Cable Current Rating
Wire temperature rise and current limits of 0.050" pitch AWG 26 gauge and AWG 28 gauge
flat ribbon cable and IDC sockets
Connections are made to most of Mosaic's embedded controllers and I/O boards using 26 AWG or 28 AWG flat ribbon cable with 0.05" pitch (wire spacing). The boards specify 24-pin headers (2 rows by 12 contacts) using 0.1" (2.54 mm) spacing. You can connect to those using 0.050"-pitch 24-wire ribbon cable terminated in an IDC socket. You may use either of the two common gauges of ribbon cable: AWG26 or AWG28. Both have sufficient current capacity for most applications.
Current in the cables and connectors generates heat, and their maximum current specification is determined by the temperature rise allowed over the ambient temperature. As a general rule-of-thumb you can count on the connection scheme supporting current capacity of up to a limit of 1 amp in each wire. However, if a current-carrying wire is bordered by wires that are not carrying appreciable current, it may have a greater current carrying capacity. This page provides the technical information needed to make the trade-offs among wire number, wire gauge, connector type, temperature rise, and current carrying capability.
Ribbon cable wire sizes
Standard 0.050" pitch flat ribbon cable usually comprises stranded 26 AWG or 28 AWG wires, but sometimes may contain wires as large as 24 AWG or 22 AWG (although AWG 22 and AWG 24 cables are uncommon). Gauge numbers are inversely proportional to wire size – every decrease in AWG number by 3 gauge doubles the wire cross sectional area and hence the wire's current capacity.
In ribbon cable the conductors are stranded, with seven strands for each. But what do AWG gauge sizes mean in terms of stranded wire?
AWG gauges specify the total cross-sectional area of a conductor whether it is made of a single strand or multiple strands twisted together. In the case of stranded wire, the area of the wire is counted, but the area of the gaps between wires is ignored. For seven circular strands twisted together thee gaps occupy about 10% of the total area; consequently, the bundle is about 5% thicker than an equivalent single solid wire.
It takes three numbers to fully specify the size of stranded wires: the overall size, the number of strands, and the size of each strand. The number of strands and the AWG size of a strand are separated by a slash. For example, a 26 AWG 7/34 stranded wire is a 26 gauge wire made from seven strands of 34 gauge wire.
The sizes and electrical properties of wires most commonly used in flat ribbon cable are summarized in Table 1.
AWG wire sizes used in flat ribbon cable | ||||||||
---|---|---|---|---|---|---|---|---|
Size (AWG) | Equivalent diameter1) | Wire resistance | Stranding scheme | Each strand diameter (mm) | Max current for chassis wiring2) (A) | Fusing current3) (A) | ||
(inch) | (mm) | (mΩ/m) | (mΩ/ft) | |||||
22 | 0.0253 | 0.644 | 52.96 | 16.14 | 7 / 30 | 0.25 | 7.0 | 41 |
24 | 0.0201 | 0.511 | 84.22 | 25.67 | 7 / 32 | 0.20 | 3.5 | 29 |
26 | 0.0159 | 0.405 | 133.9 | 40.81 | 7 / 34 | 0.15 | 2.2 | 20 |
28 | 0.0126 | 0.321 | 212.9 | 64.9 | 7 / 36 | 0.12 | 1.4 | 14 |
The fusing current shown in Table 1 gives you an idea of the current that causes a rapid dramatic destruction of the wires in the cable. Of course, operating currents must be kept much less than the fusing current!
Ribbon cable current capacity and limits
Owing to their high surface-to-volume ratio, flat ribbon cables are better than round multi-conductor cable at dissipating heat for the same conductor gauges. The side-by-side conductor geometry provides almost equally good heat dissipation from each wire with none buried in the center of a bundle of other hot conductors. Consequently, they can sustain a higher current level for a given temperature rise and conductor cross section. Further, the total number of conductors within a flat cable has little effect on the cable's overall current rating, unlike round cables where the current rating decreases dramatically as the number of bundled conductors increases.
The maximum current capacity for flat cable is potentially limited by many factors, including conductor cross sectional area (AWG), conductor composition/conductivity, thermal properties of the insulation or jacket materials, ambient temperature, air flow, and others. The essential condition is the maximum temperature rise that can be tolerated. Many insulation types start softening at temperatures greater than 100 °C, and some cable manufacturers recommend keeping cables below 85 °C at all times to prevent thermal softening of gold contacts.
Computing cable temperature rise from first principles isn't easy, but there are standard handbooks, and in particular a paper by Neher and McGrath, that are helpful4). Neher–McGrath is a method of estimating the steady-state temperature of electrical power cables. It is based on a 1957 paper5) that laid out the equations for calculating temperature rise of buried cables. Later work by CIGRE (INTERNATIONAL COUNCIL ON LARGE ELECTRIC SYSTEMS) documented an ampacity procedure into an international standard (IEC-287 and IEC-853) that provides a step-wise approach to calculating ampacity based upon cable construction.
We'll examine two sources of information for determining cable current capacity – manufacturer's specifications and actual measurements of cable temperature rise – and we'll look at how much current we can allow in individual conductors if surrounding conductors aren't used.
Cable manufacturer's current capacity specifications
Cable manufacturers determine cable current limits by considering the temperature rise over ambient temperature caused by the I2R cable loss. Generally, ribbon cables and sockets are specified for a 30 °C temperature rise when maximum current is applied to all conductors. For an additional safety margin, and to compensate for variations in cable wire thickness, manufacturers then derate the maximum current allowed by 20%.
You can easily connect to the controllers or Wildcard I/O boards using either 26 gauge6) or 28 gauge7) flat ribbon cable. The larger size, 26 gauge, can handle the greater current. For example, Belden and Assmann flat .050" pitch ribbon cables have the following current capability specifications, assuming that the full current flows simultaneously in all wires of the cable:
Part number | Wire size | Current rating8) | Resistance |
---|---|---|---|
Belden 9L26024 | AWG 26 | 1.5 A | 0.043 Ω/ft |
Belden 9L28024 | AWG 28 | 1.0 A | 0.068 Ω/ft |
Assmann AWG28-24/G/300 | AWG 28 | 1.0 A | 0.072 Ω/ft |
If all twenty-four conductors carry the full current, the following table summarizes the power dissipated by one foot of Belden 24-wire cable:
Power (W/ft) | ||
---|---|---|
Current | AWG26 | AWG28 |
0.5 A | 0.26 | 0.41 |
1.0 A | 1.03 | 1.64 |
1.5 A | 2.32 | 3.68 |
2.0 A | 4.13 | 6.55 |
The bold entries correspond to the manufacturer's current ratings of the two cables. As you can see, the manufacturer's maximum current rating, when applied to all wires in the cable, produces a power dissipation of about 2 W/ft (or 6 W/m). Presumably, at the maximum current there will be a temperature rise of the order of 30 °C
Actual measurements of cable temperature rise
Cable manufacturer 3M
has done careful measurements9) of ribbon cable temperature rise as a function of conductor size and current. They measured the temperature rise of cables both in open-air and in realistic limited-convection enclosures. They found that in order to limit the temperature rise at the center of a cable to less than 30 °C and to keep the maximum temperature below 85 °C, for internal enclosure ambient temperatures up to 55 °C, the current in the cable must be limited to the following:
Maximum Current Carrying Capacity of Ribbon Cable10) (while keeping temperature rise to less than 30 °C) | |||||
---|---|---|---|---|---|
Current Carrying Capacity (A) | |||||
Wire Size | Wire Spacing | All Conductors Carrying Current | 1-4 Conductors Carrying Current | Maximum Pulse Current | Maximum I2-% Duty Cycle |
24 AWG | 0.075 in. | 3.0 A | 4.6 A | 20 A | 2100 A2-% |
26 AWG | 0.050 in. | 1.8 A | 3.2 A | 20 A | 990 A2-% |
28 AWG | 0.050 in. | 1.5 A | 2.6 A | 20 A | 700 A2-% |
30 AWG | 0.050 in. | 1.1 A | 2.0 A | 20 A | 400 A2-% |
Of course, the actual limits for your application should be considered in light of the total heat generated, the number and spacing of cables, the expected ambient temperature, and the configuration of your system.
For example, suppose you specify your instrument to be used at room temperatures up to 40 °C (104 °F), and owing to power dissipation within the instrument its internal air temperature may rise by 15 °C, to 55 °C. Further, you want to keep the temperature of any cable or connector to less than 70 °C. You then can allow a cable temperature rise of a maximum of 70-55= 15 °C. Suppose further that only a few conductors of the cable carry significant current. From the above table you see that using 28 AWG cable you could allow up to 2.6 A per conductor for a 30 °C temperature rise. But what is the current limit for only a 15 °C temperature rise? Because the temperature rise goes as the square of the current, you are allowed a current of 2.6 × (15/30)½, or 1.84 A. For you convenience, you can use Figure 1, a graph of the cable temperature rise as a function of conductor current, to quickly ascertain allowed current for temperature rises other than 30 °C:
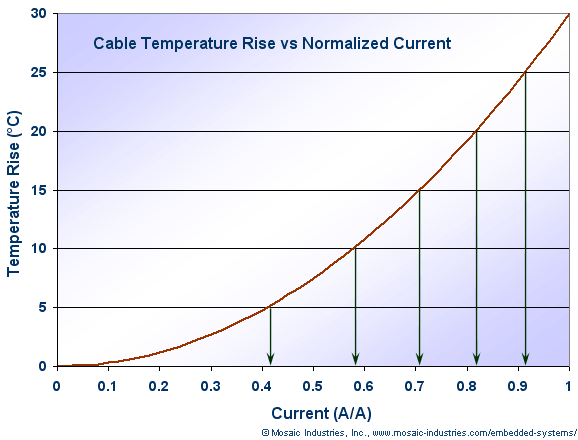
As you can see, a 15 °C temperature rise is produced by 71% of the current that causes a 30 °C temperature rise. You can use this graph to determine the current rating of the cable for other, smaller temperature rises. You should never use a cable at temperature rises of greater than 30 °C.
Rule-of-thumb for distributing current among cable wires
Of course, it is unlikely that in your application all the cable conductors will carry the same current. As the current carrying capacity of the individual wires in a cable is determined by the allowed temperature rise of the cable as a whole, it's fair to ask if it's all right to exceed the current rating of a wire if immediately surrounding wires do not carry appreciable current.
A rule of thumb is to proportion currents in the cable so that the average of the squares of the currents, averaged over four adjacent wires, does not exceed the average allowed for the cable as a whole. The squares of current are used as the heat generated in a wire is proportional to the current squared.
Using this rule of thumb,
- a single current-carrying wire in a group of four otherwise non-current-carrying wires may carry up to twice the rated current, and,
- any two in a group of four may carry up to 41% more than the rated current.
When given the choice of distributing the current among the wires in a ribbon cable, we aim to keep the total power dissipated in the cable less than 1.6 W/ft for AWG28 wire, and less than 2.3 W/ft for AWG26 wire.
These considerations of current ratings are intended as general guidelines for low power electronic communications and control applications. Current ratings for power applications generally are set by regulatory agencies such as UL, CSA, NEC, and others.
IDC connector current rating
The current carrying capacity of your connection scheme depends not only on the current capability of the wires but also the current specification of the interconnects. The current rating of most IDC sockets is 1.0A (for example Assmann IDC sockets), for all connections simultaneously. However, some sockets are capable of handling more current. In particular, the 3M™ 891 Series IDC ribbon cable socket is rated as follows,
Current capability in Amps | |||
---|---|---|---|
Wire Gauge | 1 line | 6 Adjacent Lines | All Lines |
28 AWG | 4.25 | 1.75 | 1.25 |
26 AWG | 4.50 | 2.25 | 1.50 |
Rating Conditions: EIA-364-070 Method 2, 30°C maximum temperature rise, 20% derated. |
As you can see, the current handling ability of the socket connections depends on how many adjacent high-current connections are used. The current limit for a single connection is as great as 4.5 amps, but if all lines carry equal current, the capability drops to a 1.5A limit.
The following photo (Figure 2) is of the 3M™ 891 Series IDC ribbon cable connector, rated at 1.5A per line when using AWG 26 gauge wire:
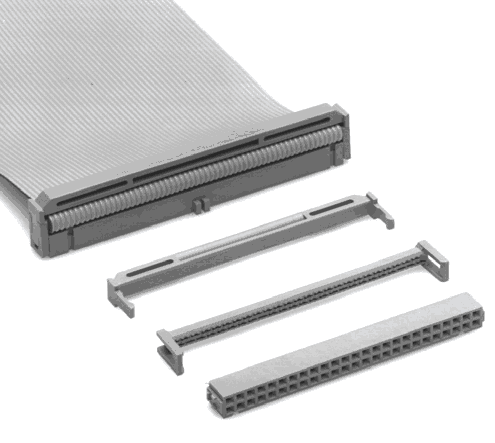
Figure 3 shows the 24-position, 3M™ 891 Series IDC socket (part number 89124-0101) we use for connecting to the field header of the Power I/O Wildcard or the PWM Driver Wildcard.
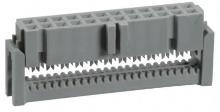
You can see the insulation displacement, tuning-fork wire contacts in this 24 position IDC socket. We use this socket with 26AWG ribbon cable in cable assembly IDC24-26AWG-24IN.
The more common 1A per line IDC ribbon cable socket is illustrated in Figure 4, a photo of the Assman connector:
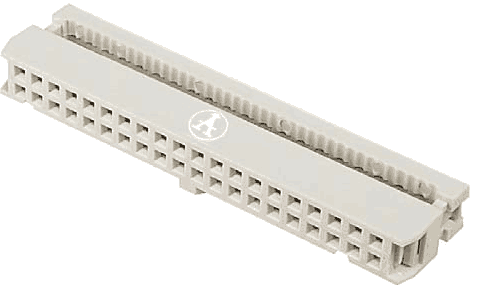
See also ⇒
- J. H. Neher and M. H. McGrath, The Calculation of the Temperature Rise and Load Capability of Cable Systems, AIEE Transactions, Part III, Volume 76, pp 752–772, October, 1957.
- 3M™ 891 Series IDC socket specifications or, if unavailable there, try here